AI in Agriculture: How Robotics and Machine Learning Are Revolutionizing Farming
Date Section Blog
A growing global population places immense pressure on natural resources and food security. To meet the increasing demand for sustainable food production, farmers, agronomists, and greenhouse operators must adopt advanced technologies.
Artificial intelligence (AI) in agriculture can drive efficiency, optimize processes, and create employment opportunities. However, AI becomes most impactful when it is scaled and integrated into daily operations.
Traditional industries like agriculture face numerous challenges, including a shortage of skilled technical personnel. On top of this, implementing advanced AI technologies has its own set of hurdles such as nature’s variability, seasonality of data, and fleet management of robots.
AI vision technologies, particularly 3D deep learning, offer solutions to scale AI in agricultural robotics by standardizing hardware and augmenting human intelligence. Robovision provides an AI platform—a versatile tool for creating, testing, and deploying AI models—that understands the variability of nature, driving actual results.
How is AI Used in Agriculture? 3D Deep Learning in Agricultural Robotics
In 2015, Robovision began leveraging machine learning and deep learning technologies in its product development. The company was a pioneer in utilizing software as a generic algorithm creation tool.
A significant challenge was extracting valuable information from real-world visualizations. After working with 2D data, it became apparent that agricultural products such as tulip bulbs, cauliflowers, and carrots required volumetric data for effective AI applications. Unlike 2D data, 3D data provides a richer environmental understanding, improving machine decision-making. 3D deep learning AI models are the most efficient way to deploy AI into agriculture robots.
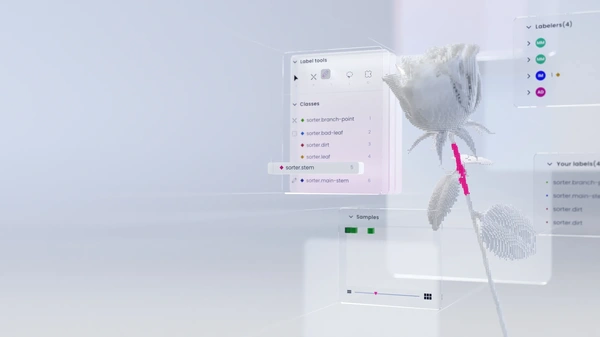
AI Applications in Agriculture
The food industry is at a crossroads, with increasing risks driven by resource scarcity and population growth. The development of 3D deep learning technology is revolutionizing agricultural robotics and allowing for broader use of AI throughout farm and food production automation.
For example, Robovision is collaborating with Iris Stick to develop smart glasses powered by NVIDIA hardware, which help greenhouse operators efficiently identify ripe tomatoes and other crops. Combining 3D deep learning with hyperspectral imaging will further enhance the capabilities of vertical farms, driving more efficient food production processes.
How Are Robots Used in Agriculture?
Robovision pioneered the introduction of a new generation of planter machinery capable of planting various types of tulips. This success marks just the beginning. The company is expanding its use of 3D deep learning technology to tackle more complex challenges in agricultural robotics. There are many AI in agriculture examples, but below are several key applications:
- Automated Sorting: Agriculture robots use 3D deep learning to autonomously sort products like fruits and vegetables by size, shape, and color, improving efficiency and reducing labor costs.
- Plant Cutting: Robotics in agriculture automate plant-cutting tasks, such as rose cutting, with precision. For example, Robovision’s rose-cutting technology, utilizing 3D deep learning, can cut up to 1,600 roses per hour at the exact correct angle, enhancing both the speed and accuracy of the process while maintaining quality.
- Phenotyping: AI in agriculture enables automated assessment of plant traits, like health and growth patterns, for more accurate breeding and crop selection.
- Vertical Farming: AI applications in agriculture optimize growing environments, monitor plant health, and boost crop yields using 3D deep learning and hyperspectral imaging.
AI Solutions for Agriculture: Tackling Deployment Challenges
AI has the potential to significantly scale food production in agriculture, but its adoption faces key challenges: reducing technical barriers in production, nature’s variability, seasonality of data, and fleet management of robots in agriculture.
Challenge 1: Reducing Technical Barriers
Robovision’s platform was designed to help farmers and greenhouse workers who lack technical expertise manage AI projects. The platform allows domain experts on the ground with no IT knowledge to label images and deploy these datasets in just 15 minutes.
Robovision includes 3D annotation capabilities that go beyond traditional 2D labeling, offering specialized tools for agriculture, such as lasso, connectivity, and direction. These advancements have benefited both the agriculture and healthcare sectors.
For example, Robovision’s Rose Cutter uses an intuitive AutoCAD-like interface allowing farmers to train AI models to understand plant characteristics and reduce dependency on support teams.
Challenge 2: Variability of Nature
Agriculture’s natural conditions—such as humidity, drought, and floods—introduce considerable variability, making each farming environment unique. Robovision’s AI solutions for agriculture make it easy for operators to quickly adapt AI models to these changes.
By labeling plants in 2D or 3D, operators can retrain and deploy new AI models. The process is simple: within minutes, operators can update the AI models with more visual data to reflect the new environmental conditions. This flexibility allows agriculture robots and machinery to adjust rapidly without requiring specialized technical knowledge.
The platform empowers thousands of clients to develop AI models independently, creating new opportunities and reducing reliance on in-house data scientists.
For example, Forensics, an integrator of Robovision’s machine-building partner ISO Group, uses NVIDIA GPUs to retrain 3D deep learning networks. This allows AI models to adapt to the specific growth patterns of tulip bulbs, providing a key example of how machine learning in agriculture can help optimize production for specific plant types and conditions.
Challenge 3: Seasonality of Data
Agriculture’s seasonality can delay the implementation of automation systems. If an AI project isn’t perfected within a growing season, companies must wait until the next cycle.
Robovision overcomes this challenge by using synthetic data. This method allows the company to simulate various environmental conditions—such as drought or plant size—without waiting for real-world validation. Supported by over 150 NVIDIA GPUs, Robovision can generate simulated data to reflect different conditions and prepare AI models for real-world applications.
Challenge 4: Fleet Management of Robots in Agriculture
Managing fleets of robots and drones requires efficient AI model deployment. Robovision’s platform simplifies fleet management by providing full AI lifecycle support. Features like test automation and DevOps scripts help companies scale AI systems without requiring large teams of data scientists.
More than 600 robots in over 40 countries run AI applications developed with Robovision’s platform. Operators, farmers, and greenhouse managers can independently train and scale 3D deep learning models, taking full ownership of the process.
Machine Learning in Agriculture: How Robovision Paved the Way
Robovision’s platform empowers farmers, agronomists, and greenhouse operators to create AI models by creating and using their own data, without requiring data scientists. These AI models can be deployed on greenhouse automation systems or agriculture robots.
One of Belgium's fastest-growing tech companies, Robovision employs over 120 engineers and data scientists. Originally, it operated as a consultancy, focusing on creating flexible machines that combined robotics with camera acquisition devices.
After launching the first series of machines, demand grew for products capable of adapting to various plant types and conditions. This shift in demand led Robovision to develop a scalable AI-powered platform that enables businesses to overcome scalability challenges in agriculture automation.
The future of AgTech, from our perspective, is standardised hardware and scaling expert knowledge. With expert knowledge, we meant domain experts or non-technical operators that can use a self-serving and uncomplicated AI platform to annotate complicated plants like roses or tulips and be able to manage these AI workflows by themselves.
Jonathan Berte, CEO of Robovision
Benefits of AI in Agriculture Are Undeniable
The future of agricultural technology lies in standardized hardware and scalable expert knowledge. With Robovision’s self-service AI platform, farmers and operators can annotate complex plants like tulips or roses, manage AI workflows independently, and scale operations as needed.
The more data is annotated, the better the AI models become, enabling farmers to train new plant types using global annotation pools. By leveraging 3D deep learning, Robovision’s platform supports scalable AI operations in agricultural robotics, driving efficiency and growth in the AgTech industry.