AI-Powered Quality Control in Injection Molding
Niko Group partnered with Robovision to enhance quality control by integrating computer vision AI into its injection molding process, resulting in a highly efficient automated quality check and significantly reduced production waste.
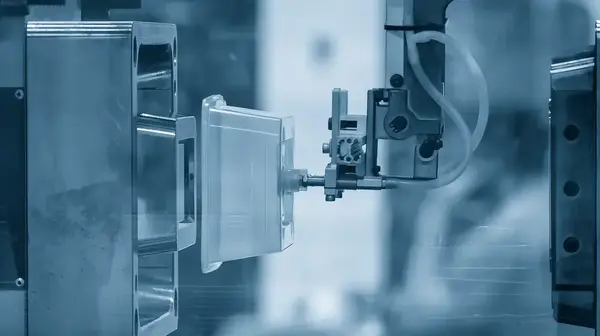
Quality control in manufacturing
With a product range of over 5,000 products, Niko Group is Europe’s leader in electric(on)al components, from switches to sockets. Every week, over 200,000 pieces of their most popular product come rolling off the conveyor belt. Quality control is a crucial final step of the manufacturing process.
Automating manual quality control
Niko had a traditional quality control system in place. Inspecting each finished item manually was very time-consuming. Moreover, the system yielded too many false positives as well as false negatives. In other words: a lot of good pieces were being thrown out, while the bad ones were left to continue their journey.
Enhancing the quality control process with AI
AI proved much more accurate than Niko’s existing solution. Robovision’s Computer Vision AI application reduced the number of misshapen pieces that passed quality inspection by 33%. For the good pieces previously wrongly accused of defects, the number even shot up to 72%--meaning that far fewer products are thrown away unnecessarily.
AI platform is easy to train for new products
Added bonus: it takes Niko just a few hours to train their AI application to recognize faults in a new product type, compared to weeks using a traditional vision system. An important asset to stay ahead in a competitive market.
Read the story on Niko's website.