Visual Food Inspection: How AI is Transforming Food Manufacturing
Date Section Blog

Visual food inspection is essential for maintaining food safety, quality, and regulatory compliance. Traditionally, the food industry has relied on manual inspection due to the natural variability of food products—pears, even within the same species, can vary in size, color, and shape. Humans have historically been the only ones capable of distinguishing between normal variations and actual defects.
Advancements in vision technologies, particularly AI, are revolutionizing visual food inspection. Unlike traditional vision systems that rely on consistent properties to detect anomalies, AI-powered systems can learn and adapt to the vast variability in food.
What Is Visual Food Inspection?
Visual food inspection refers to the process of examining food products for defects, contamination, and overall quality assurance. Generally, there are four types of quality inspection: pre-production inspection, during production inspection, pre-shipment inspection, and loading/unloading inspection.
When it comes to visual food inspection, manual observation has proven to be the most effective method. Technologies are quickly evolving with innovations in machine learning algorithms and AI computer vision—AI essentially understands food inconsistencies faster and more accurately than humans.
Types of Visual Food Inspection
Different approaches to visual food inspection emerge as food production scales, skilled labor becomes harder to find, and regulations become stricter. While the food industry has relied on manual methods for years, AI-driven systems are rapidly transforming the landscape.
Below are the four main types of visual food inspection, each offering distinct advantages depending on the application.
- Direct Visual Inspection – Human-based observation.
- Indirect Visual Inspection – Utilizing tools such as magnification devices and cameras.
- Automated Visual Inspection – Traditional machine vision systems detecting pre-programmed defects.
- AI-Powered Visual Inspection – Advanced systems leveraging deep learning to identify complex food anomalies.
Technologies Used in Visual Food Inspection
Vision and imaging technologies have long played a crucial role in food inspection. Today, a key challenge lies in enhancing these systems with state-of-the-art AI technology to improve accuracy and adaptability.
Machine Vision Systems
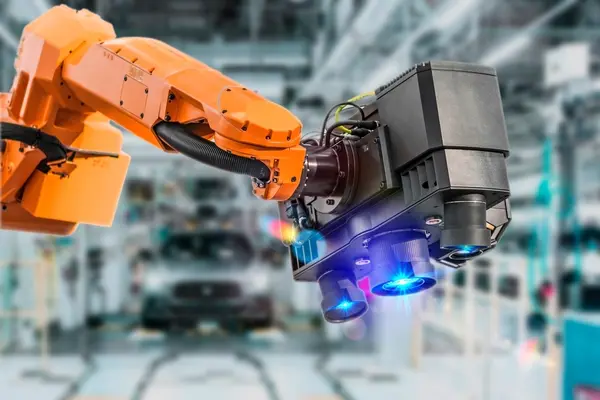
High-speed cameras and sensors capture detailed images of food products or packaging for real-time defect detection and quality control. Structured lighting, advanced optics, and calibrated lenses are used to identify inconsistencies in size, shape, and color.
By relying on predefined parameters, traditional machine vision systems can efficiently sort products, flag defects, and ensure quality standards are met. That said, machine vision struggles with natural variability in food products, often misclassifying acceptable variations as defects and lacking the adaptability to detect more complex or unexpected issues.
X-Ray and Spectroscopy
X-ray inspection and spectroscopy are advanced imaging techniques used to detect contaminants that are not visible to the human eye, such as metal, glass, and bone fragments.
Used for identifying foreign objects within processed and packaged foods, this technology ensures safety and compliance with industry regulations. On their own, x-ray and spectroscopy vision systems still struggle to distinguish between naturally occurring variations in food products and actual contamination, leading to occasional false positives or missed defects in organic materials.
AI and Machine Learning Integration

AI significantly enhances traditional food inspection technologies by adding adaptability and learning capabilities that conventional systems lack. Traditional machine vision, for example, can detect surface-level defects on baked bread, such as an irregular shape or a burnt crust.
AI-powered deep learning models can go further by analyzing texture, air pockets, and subtle color variations to classify multiple defect types, predicting potential quality issues before they become problems. Beyond simply identifying a "burnt crust," AI can assess the doneness of a loaf of bread on a scale from 1 to 5—for example, with 1 indicating undercooked, 3 representing perfectly baked, and 5 signifying burnt.
- AI Capabilities: AI can adapt to natural variations in food products, reducing false rejections and improving defect classification. By learning from vast datasets, AI models continuously improve their accuracy, ensuring fewer quality control failures.
- Deep Learning Models: These models train on vast visual datasets, learning from real-world examples to improve detection accuracy over time, making them highly adaptable. Unlike traditional systems, they do not require rigid pre-programmed rules, allowing them to recognize unexpected or emerging defects.
- Real-Time Quality Monitoring: AI enables continuous oversight, and can adjust on the fly to optimize production and reduce waste. It detects trends in defects and can make real-time recommendations to modify production settings, preventing widespread quality issues before they escalate.
Benefits of AI-Powered Visual Food Inspection
AI-powered food inspection brings numerous advantages that traditional methods cannot match, driving higher accuracy, efficiency, and overall quality control improvements.
- Enhanced Food Safety: AI detects contaminants with high precision, identifying microscopic foreign objects or anomalies that human inspectors and traditional systems might miss.
- Greater Efficiency and Automation: AI is fast and provides real-time insights, reducing production bottlenecks and minimizing labor costs while maintaining product and quality consistency.
- Waste Reduction: AI minimizes false rejections by distinguishing between true defects and natural product variations, preventing unnecessary food waste, and optimizing resource use.
- Improved Packaging Integrity: AI-driven inspection ensures that food packaging is sealed properly to reduce contamination or spoilage. AI detects label misprints and omissions, reducing compliance risks and protecting consumers from misleading ingredient information.
- Better Consumer Trust: Ensuring consistent quality builds brand reputation, reducing recalls and reinforcing consumer confidence in food safety and reliability.
Robovision: AI Visual Food Inspection
For 15+ years, Robovision has been turning automation challenges in food production into advantage with vision AI. Designed to understand the vast variability of organic food products, it streamlines quality control, informs intelligent robotics, and integrates with existing hardware.
Robovision offers:
- Grading and Sorting: Identify size, shape, color, and surface quality of food items on fast-moving production lines, sorting them according to quality standards defined by the user.
- Anomaly Detection: Detect foreign materials like plastic fragments, glass shards, or metal pieces on fast-moving conveyors, minimizing the risk of contamination.
- Intelligent Robotics: Guide robotics and machinery to remove foreign objects, as well as damaged or poor-quality food items, for consistency and quality.
The Future of Food Inspection: Vision AI at the Forefront
Companies adopting AI-driven food inspection systems gain a competitive advantage in quality control and regulatory compliance; AI enhances traditional visual food inspection by improving defect detection, reducing waste, and increasing efficiency.
By integrating real-time monitoring and deep learning, AI brings unparalleled precision and scalability to food safety. These intelligent systems continuously learn and adapt, making real-time decisions that enhance compliance and build consumer confidence.
The future of food inspection is not just about meeting standards—it is about setting new benchmarks in quality, efficiency, and reliability through automation and data-driven intelligence.
Frequently Asked Questions: Visual Food Inspection
Visual inspection can identify a range of defects and quality issues, including contamination, discoloration, irregular shape, surface damage, foreign objects, and improper packaging. Traditional methods rely on human inspectors or simple machine vision, while AI-powered systems enhance accuracy and consistency by detecting subtle variations that might be missed manually.
AI reduces costs by automating the inspection process, significantly cutting labor expenses and minimizing human error. It enables real-time monitoring, reducing the need for manual intervention while improving throughput. Additionally, AI-driven systems optimize defect detection, decreasing waste and recall costs by ensuring only truly defective products are discarded.
While AI-powered vision systems excel at detecting a wide range of defects, including physical contamination, irregularities in texture, and packaging issues, they have limitations with certain internal defects, such as hidden contamination that requires chemical analysis. However, when integrated with technologies like X-ray and spectroscopy, AI enhances detection capabilities for a more comprehensive inspection.
AI contributes to sustainability by reducing food waste through more precise defect detection, ensuring that fewer products are unnecessarily discarded. It also improves efficiency in processing, lowering energy consumption and resource use. Additionally, AI helps maintain packaging integrity, preventing spoilage and extending shelf life, which reduces overall food waste in the supply chain.