Improving Battery Quality with Robovision’s Defect Detection and Classification Solutions
Date Section Blog
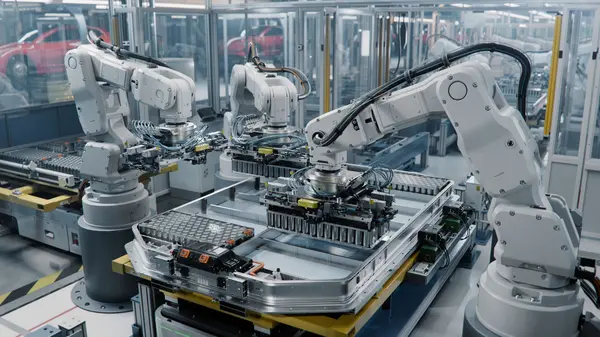
In battery manufacturing, detecting surface defects in critical components—like electrodes and separator layers—makes the difference between producing batteries with optimal product performance, safety and longevity, and waste. Fewer defective batteries continuing down the production line preserves energy and saves material costs, making well-built early defect identification systems indispensable.
The Challenge of Surface Defect Detection
Surface defects, such as cracks, uneven coatings, and pinholes (to name just a few) have a direct impact on battery efficiency and safety. Current inspection techniques, like optical microscopy or scanning electron microscopy (SEM), provide detailed analysis but usually require offline sample preparation, making them unsuitable for in-line production.
Surface defect detection is especially challenging in the ramp-up phase of new battery production facilities. In this phase, a multitude of process parameters, such as the composition of the raw material used to create electrode sheets, needs to be tuned. Immediate feedback on the presence and nature of surface defects on the electrodes is required to assess the impact of such process parameters on the quality of the batteries produced.
Vision AI offers a scalable solution to assess the quality of batteries produced, thanks to real-time surface defect detection during production. But as battery layers present a wide variety of potential defects, building an effective Vision AI model requires extensive datasets to train and validate robust algorithms.
Additionally, delivering a Vision AI solution for battery manufacturing requires integrating with the camera and IT systems on the production floor. Adding camera capabilities to a production floor IT system enables linking insight gathered on the presence and nature of surface defects to both the production process parameters upstream and the battery quality metrics identified downstream.
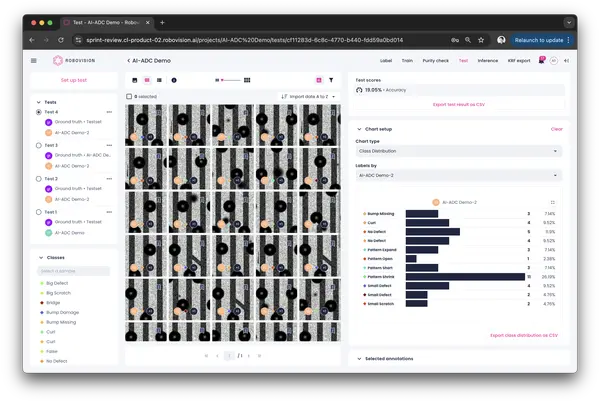
Robovision’s Solution for Surface Defects
The Robovision AI Platform is designed to scale Vision AI applications in demanding and dynamic environments, providing battery manufacturers with practical tools to optimize and expedite the production ramp-up of their factories.
The platform has a proven track record in defect detection and classification on wafers in the semiconductor sector, which shares notable similarities with the battery layer inspection. The labeling process of large datasets has been repeatedly described by customers as "tedious” and realistically “impossible”—until using our solution. By adopting workflows such as predictive labelling, customers can set up Vision AI models starting from limited data, deploy the models within the production environment, and incrementally improve quality by capturing and labelling new data using the Purity Loop.
The platform allows for central Vision AI model creation and management. Models can be deployed to edge devices close to the production lines and generate real-time insight on the types and kinds of defects. The resulting feedback improves the platform's models further. By coupling the platform to other IT systems within production environments, manufacturers can link numerical insights directly to process parameters.
The Robovision AI Platform is built for scale and supports large amounts of production inspection points, bringing considerable benefits to large scale product facilities such as battery gigafactories. This implies that once the model reaches maturity, its logic can easily be replicated across multiple inspection lines, ensuring consistent thresholds globally—unlike competitive solutions which typically require retraining each edge device for every inspection line.
The Road Ahead
For battery manufacturers, implementing advanced Vision AI solutions like Robovision’s platform represents a significant step forward in quality assurance. By leveraging efficient defect detection and classification, manufacturers can enhance product reliability, reduce waste, and meet the growing demand for high-quality batteries. In short that means higher yield and lower cost.
Robovision is committed to improving battery manufacturing quality and continually improving its platform (optimizing both defect detection and classification tools) to better meet the demands of the battery industry. As new datasets and insight emerge, the platform’s capabilities will continue to evolve, providing a scalable, efficient, and powerful solution for one of the industry’s pressing challenges. In battery manufacturing, the only good waste is less waste.
Want to learn more about how Vision AI can transform your battery inspection process? Contact Robovision today to explore the possibilities.