Battery Quality Assurance Strategies: Key Steps for Manufacturers
Date Section Blog
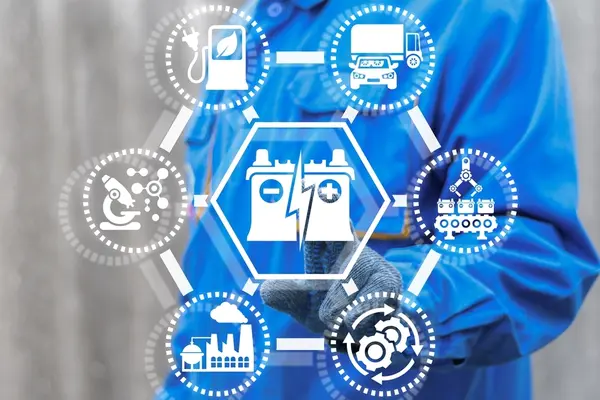
Battery quality assurance secures the reliability, safety, and performance of energy storage solutions. A strategy centered on automation and digitalization supports rapid scaling and answers some of the biggest challenges today’s manufacturers face, while advanced technology and predictive quality measures pave the way for consistent product excellence.
The Criticality of Quality Assurance
Battery quality is among the most problematic issues facing the industry today. Yet the human, financial, environmental, and reputational stakes are immense. Unprecedented pressure comes from EV makers, electrification and decarbonization initiatives, investors, and fierce competition amidst market volatility. Manufacturers must also contend with process complexity and gigawatt-hour-scale production, making innovation key to achieving product reliability, volume, and cost savings. To achieve this and accomplish end-to-end battery quality, several key steps should be implemented into strategies.
Closed-Loop Quality Management
Integrating holistic quality management across the battery product lifecycle enables manufacturers to scale and stabilize production in a challenging market. It is essential for achieving safe, high-quality, and environmentally friendly products. A closed-loop approach applies to design, engineering, manufacturing, use in the field, and back in a virtuous cycle for continuous improvement — supporting every phase of the product lifecycle:
Overall project management – Plan with product quality in mind and to help deliver projects on time
Failure mode and effects analysis (FMEA) – Evaluate design and process risks in the early development and planning stages. Combine FMEA with variation analysis to optimize design, tolerances, and assembly processes early in the product development phase.
Control and inspection planning – Plan and optimize the management of quality inspections
Problem-solving process with root-cause analysis – Create a workflow-guided, standardized problem-solving process using root-cause analysis tools
Quality action management – Allow on-time delivery of actions and escalation management
Audit and assessment – Identify and eliminate redundant activities to streamline processes, saving time and resources
To accelerate safe, reliable battery production, a culture of quality should feature consistently throughout each phase of battery development and production, starting with design.
Virtual Product Design
Balancing performance and cost through virtual product design is a cornerstone of any battery quality assurance strategy. Engineers analyze thermal management, electrochemical performance, and mechanical stresses under various conditions by simulating physical behavior and rapidly validating designs. This approach identifies potential issues and optimizes designs before building physical prototypes, saving time and resources.
Quality Execution and Control
Virtual execution of control plans is a digital and holistic approach that enforces preventive practices. It minimizes human error and quickly moves the production line to a stable quality level. To improve this and implement predictive control, manufacturers harness advanced data analytics integrating process parameters, image processing, product performance controls, and environmental context. Machine learning algorithms are also used to optimize precision across production processes. Ultimately, the goal is to reach the prescriptive level. Securing product quality at this stage involves injecting data analytics into simulation models to calculate and apply corrective actions on-the-fly.
Rigorous Inspection Techniques
While strong design and control execution processes reduce the risk of battery defects, they do not eliminate them. To further mitigate risk, rigorous testing should be deployed across the production process. This includes first-article inspections at the start of production to verify the quality meets requirements. In-process inspection ensures manufacturing processes and techniques are correctly followed. While pre-shipment inspections control the quality of batteries and identify defects before shipping.
Each stage requires comprehensive testing protocols, such as in-process inspection to verify cell consistency and performance. These methods help detect defects early in the production cycle. Common testing and inspection procedures for this stage include:
- Environmental testing: Batteries are subjected to extreme temperatures and humidity to simulate real-world conditions
- Thermal and vibration testing: Stability is evaluated under mechanical stress
- Electrical performance tests: Measurement of capacity, charge cycles, and discharge rates
Standardized procedures and frequent audits align testing with regulatory requirements. Test results should be recorded and analyzed, with numerical insights linked to process parameters. This systematic approach supports high-quality outcomes across large-scale production lines.
Automation That Boosts Efficiency
Automation enhances production efficiency and scalability. Implementing advanced manufacturing systems such as automated production lines, robotics, and AI-driven quality control systems reduces manual labor, minimizes errors, and boosts output and consistency. Another example is the integration of automated testing systems and feedback loops. Both provide immediate feedback and adjustments to production processes, enhance overall product reliability, and reduce waste.
Advanced Technology Integration
Advanced technology like vision AI takes automation to the next level. It enhances robot and machine inspection capabilities, maintaining flawless production and maximum efficiency with unmatched accuracy in surface defect detection. Inspection systems using real-time adaptive vision AI automate the inspection process and detect everything from streaks to oil stains, pinholes, to burrs across every stage of production—all at industrial speeds. Key technologies include:
- High-resolution imaging: Cameras capture microscopic anomalies during production
- Machine learning algorithms: AI models gather visual input, apply deep learning algorithms, analyze results, and instruct machines accordingly.
- Predictive analytics: Data models forecast quality issues based on historical trends, identifying imperfections before they cause assembly failures
These systems operate at the edge and provide immediate insight into production quality. When inspection tools are combined with centralized data platforms, real-time performance monitoring across multiple lines proactively drives consistency and continuous improvement.
Continuous Improvement Through Data Analytics
Data analytics is at the heart of modern quality assurance strategies. Extensive data is collected from each production stage and used to analyze performance trends to help identify potential bottlenecks and potential issues. The following approaches achieve this:
- Feedback loops: Automatic alerts signal deviations in production parameters
- Statistical process control: Monitor key metrics to adjust testing protocols
- Predictive maintenance: Use of data trends to anticipate equipment malfunctions
Regular analysis of testing outcomes provides insights that inform incremental process improvements. The cycle of testing, analysis, and adjustment fosters a culture where quality becomes self-reinforcing—improving yield and reducing waste as adjustments occur in near real-time.
Future Trends in Battery Quality Assurance
Looking ahead, battery quality assurance strategies must evolve with technological advancements and market demand. Equally important is adapting to future trends that will redefine industry standards, such as the development of advanced materials to enhance battery thermal stability. Although lithium-ion batteries currently dominate the EV market, the rise of alternative chemistries such as solid-state, sodium-ion, and lithium-sulfur are gaining traction. And as battery technology advances, regulatory bodies worldwide enforce stricter safety standards. The evolution of efficient energy storage signals tighter quality controls and more complex production environments. Manufacturers can respond and succeed with scalable, data-driven strategies that guarantee consistency and satisfy strict global regulatory standards.
Quality That Powers up the Future
Battery quality is one of the greatest barriers to accelerating battery production. To overcome this, quality assurance is vital to ensuring reliable and safe energy storage solutions. Manufacturers can avoid the high costs associated with waste, recalls, and rework with holistic best practices applied throughout production. This emphasizes the criticality of quality management in achieving manufacturing success. Companies that invest in these key steps along with the advanced technology solutions not only protect their operations, they cement their reputation in a competitive global market.
Ready to see how Robovision optimizes battery production from start to finish? Learn more here.