Stop Guessing, Start Adapting: AI Retraining for Smarter Food Processing
Date Section Blog
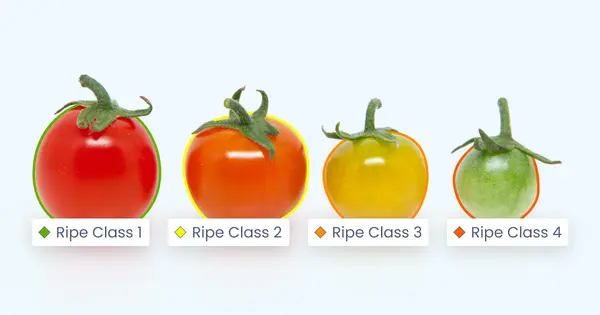
Businesses expect AI-based sorting and inspection systems to maintain high accuracy over time. During the proof of concept (POC) or pilot phase, AI models often deliver impressive results, reaching high-performance levels quickly. But once deployed in real-world production, a hidden challenge emerges—gradually, AI begins to quietly misclassify products.
At first, the issue seems small. A few tomatoes are sorted incorrectly. A batch of berries is flagged for defects that were not a problem before. Over time, these errors multiply, reducing efficiency instead of improving it. The model isn’t “broken”—it’s simply outdated.
AI models do not stay accurate forever. Without structured retraining, updates become a manual burden, causing data chaos, performance decline, and inefficiencies. Retrainability is crucial, but a well-managed AI system is key to preventing long-term failure.
What Is Retrainability in AI?
AI models do not operate like fixed-rule systems. They learn from data, and that data represents a specific moment in time—what “good” and “bad” products, or certain defects, looked like when the AI was first trained.
But products, especially food products, are never truly static. Ripeness levels shift with the seasons. New varieties enter the market. Product defects change. An AI model trained previously may no longer match today’s reality.
When your model’s accuracy is declining, it’s not because your model is bad, but because the objects it sees aren't adequately represented in its original dataset anymore.
Rob Gielen — Robovision Market Director, Agri & Food
Retrainability is the process of updating an AI model with new, relevant data so it continues to perform accurately. However, if retraining is not structured and systematic, there is a risk of making models worse instead of better.
Why Retrainability Matters: The Role of Variability in Food Processing
Retraining is a necessity to maintain accuracy and competitiveness in every industry using AI. Food processing presents unique challenges that increase the need for ongoing updates.
Unlike manufactured products—such as coffee mugs, which are produced from the same mold—food products are naturally variable. Even within the same category, no two tomatoes or blueberries are identical.
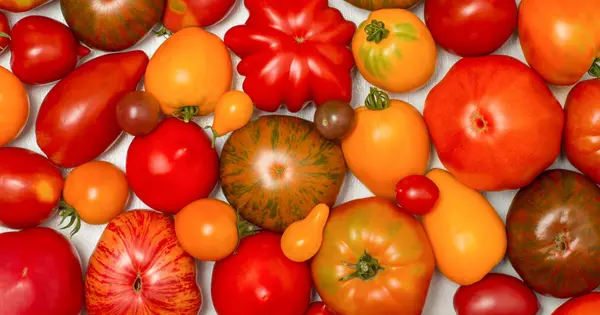
Several factors contribute to this constant change:
- Climate and Seasonality – A tomato grown in Spain in July looks different from one grown in the Netherlands in December. An AI model trained on last year’s data may struggle with this year’s produce.
- Evolving Consumer Preferences – Cherry tomatoes were a niche product 20 years ago; today, they dominate supermarket shelves. New varieties emerge, requiring AI models to adapt.
- Regulatory and Quality Standards – Depending on the target market, quality expectations vary; high-value markets require AI to detect finer defects, while others allow more variance. Retraining is needed to meet evolving quality standards.
How to Approach Retraining: Different Strategies
Not all AI providers handle retraining the same way. Businesses typically follow one of four approaches, each with its own advantages and drawbacks.
The "Supermodel" Approach
Some companies attempt to build a universal AI model that can function without retraining. This requires collecting massive datasets over a long period of time before the AI is even deployed.
For example, certain companies spend years gathering data from major farms to build a sorting system that works across all production lines without needing updates.
✅ Pros | ❌ Cons |
---|---|
Works well in highly controlled environments where product variation is minimal | Takes time to develop, is expensive, and cannot adapt to new product variations or market changes. |
The "Continuous Retraining" Approach
Instead of relying on a universal model, businesses can deploy AI models quickly and refine them over time based on real-world data. This approach works well for food processing, where variability is constant.
✅ Pros | ❌ Cons |
---|---|
Highly adaptable and scalable across multiple facilities and production lines. | Requires strong AI management tools to prevent dataset chaos and retraining errors. |
Periodic Manual Retraining Approach
Some businesses retrain models at scheduled intervals—for example, every six months or once a year.
✅ Pros | ❌ Cons |
---|---|
Lower retraining costs compared to continuous updates. | Accuracy drops between retraining cycles, making it unsuitable for industries with constant variation, like food processing. |
Hybrid Approach
In this method, companies start with a pre-trained AI model based on a broad dataset (e.g., many types of fruit) and fine-tune it over time for specific customer needs.
✅ Pros | ❌ Cons |
---|---|
Faster deployment than a fully custom model, while allowing ongoing adaptation. | Still requires structured retraining management to prevent errors. |
How Robovision Manages Retraining Effectively
AI retraining only adds value if done systematically and efficiently. Without a structured approach, food processors risk collecting irrelevant data, mislabeling defects, or deploying updates that worsen performance.
Robovision’s targeted retraining ensures AI models adapt to real-world food production variability without creating dataset chaos. This is achieved through intelligent data capture, centralized model management, and structured version control.
Intelligent Data Capture and Monitoring
In food processing, AI models must distinguish subtle variations in produce—ripeness, size, color, and surface defects. Robovision’s inference monitoring continuously tracks model accuracy in real-time production settings. A customizable dashboard alerts operators when data drift occurs, so retraining happens before sorting errors affect efficiency.
One major pitfall in AI retraining is collecting millions of redundant images—a waste of storage and processing power. Robovision avoids this by capturing only the most relevant data—cases where the AI struggles.
What you don’t want is a million images of tomatoes where 99% show things your model already works well with. You want the images where your model is flawed—those are the ones that will actually improve it.
Rob Gielen — Robovision Market Director, Agri & Food
By filtering only essential training data, Robovision keeps AI models precise, adaptable, and cost-efficient for food production environments.
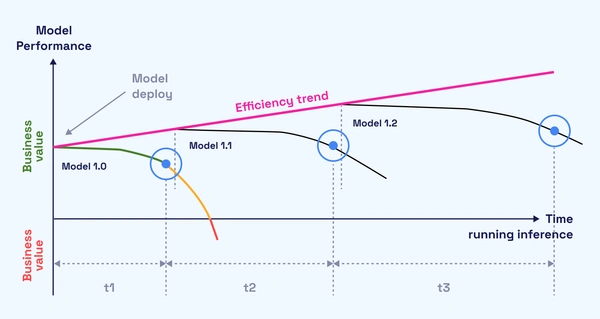
End-to-End AI Management: Hub and Spoke Model
AI retraining is not just about collecting data—it is about managing AI models, especially if deployed across multiple production sites. Food processing plants deal with seasonal variations, shifting quality standards, and multiple product lines, making AI model management complex.
Robovision addresses this with a hub-and-spoke AI management model:
- Central Hub – AI models are trained, updated, and version-controlled in a structured system: retraining remains organized.
- On-Site Model Monitoring – AI doesn’t just run in the cloud, it operates directly in food processing plants, adapting to real-time product variations.
- Automated Retraining Triggers – When the system detects accuracy drift, it flags the need for retraining, ensuring problems are addressed before they impact production.
Unlike manual AI solutions, which require guessing when retraining is needed, Robovision provides an automated process to maintain long-term AI accuracy across food processing lines.
AI-Assisted Labeling & Version Control
Retraining only works if new data is labeled correctly—especially in food processing, where defects can be subtle (e.g. minor bruising, early mold growth). Poor labeling results in models learning the wrong patterns, leading to performance declines.
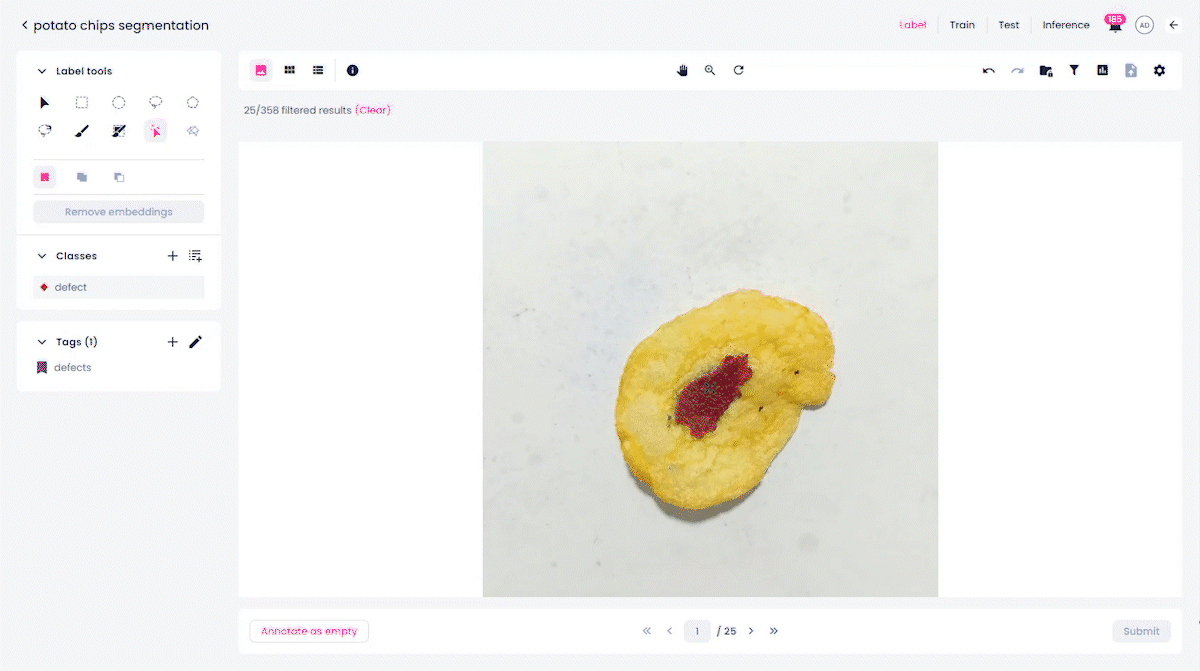
Robovision provides:
- AI-assisted labeling – A large vision model (LVM) detects contours and generates precise image masks, reducing manual labeling time without sacrificing accuracy.
- Version tracking and accountability – Every model update is logged, including: who labeled the data, whether labels were reviewed and approved, how retraining impacted model accuracy.
- Rollback capability – If a retrained model performs worse than its predecessor, operators can pinpoint errors and restore a previous, better-performing model.
Without a structured system, food processors risk deploying faulty AI updates with no clear way to correct them.
Retrainability Should Be a Core AI Selection Criterion!
Many food processing companies don’t realize the need for retraining until AI grading fails—sometimes years after deployment. Different retraining strategies exist, but any AI solution without structured retraining management will eventually struggle.
Before selecting an AI provider, food processors should ask:
- How does this system handle retraining?
- Does it prevent dataset chaos?
- Can retraining be tracked and managed systematically?
The right AI solution doesn’t just retrain—it ensures long-term accuracy, adaptability, and scalability, keeping food production efficient and precise.